TK80/BSの
シンセシステムを復活/拡張したい~
その12
DCOの不具合検出基板、新モジュール作製
2017年
8月26日
マルツで購入したDCOの不具合検出基板の部品です。5Vに12V系が乗ってくるので、どのチャンネルのDCOが悪いのか調べます。
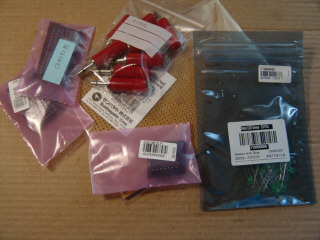
作製途中です。回路はコンパレータ、ラッチ、ダイオードを使ったOR回路、4013のD-FFです。4ビット分、配線が終わったところで、動作確認します。モニタ電圧が6.5Vを超えるとLEDが点灯して保持されます。動作良好です。
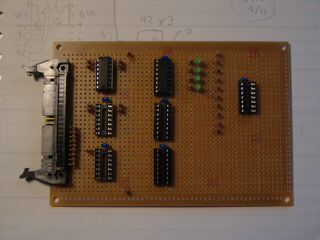
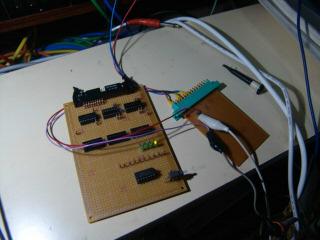
8月27日
9ビット分完成しました。DCOが8ビット、データ変換ボードが1ビットです。裏はジュンフロン線で半田付けでこんな感じ。
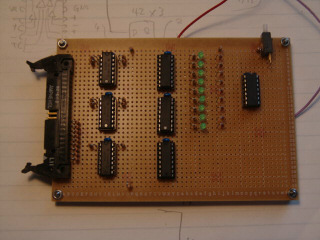
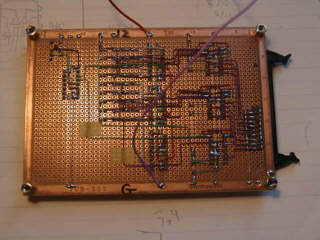
DCOと不具合検出ボードはフラットケーブルで接続します。先端には3.5mmのプラグを取り付けました。
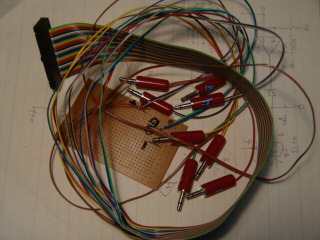
DCOボード側も修正します。手持ちのショットキ(CMS02)を5Vラインに入れて、モニタ電圧をパネルまで配線します。
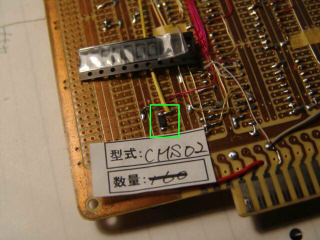
DCO4台で動作確認中。モニタ電圧は使用していない、基本周波数の64倍のPLL出力のジャックから出力します。
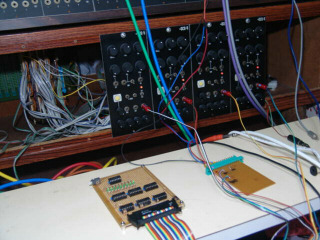
VCA横の新モジュールのパネルに部品を取り付けて、基板を取り付けるアルミ板の型を厚紙で作製しました。
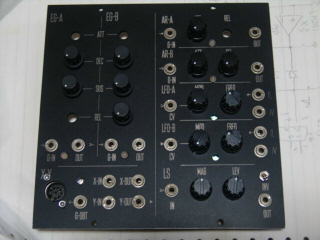
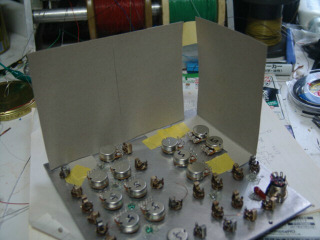
こちらはaitendoで購入した128x64ドットのLCDです。MSP430でUSBーMIDIー>MC80インタフェース変換基板を作る予定です。PCからもこのシステムが鳴らせるようにしたいです。
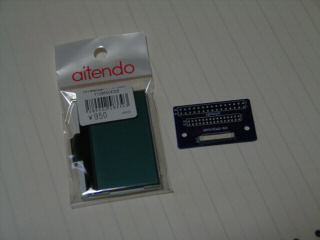
DCO8台とデータ変換基板、合計で9ビット分モニタ中です。検出基板の電源は上部のアナログシンセサイザから分配します。
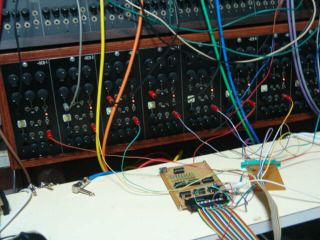
現象が発生しました。DCOのCH7の5Vが11Vになっています。複数回現象が出て、いずれも同じCH7です。現状はLEDが点灯したら、手動でDCOの電源を切りますが、SSRを追加して自動的にDCOの電源を切ることもできます。
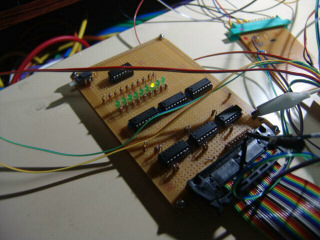
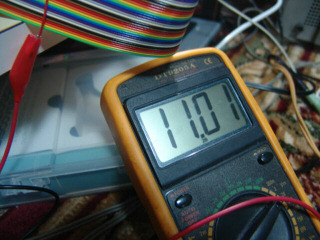
9月4日
こ
の週は遅い夏休みです。DCOの不具合ですが、デバイスには12V系を5Vに通すようなパスが無いため、デバイス以外の原因を考えてみます。デバイス以外に可能性があるの
は電源と基板です。電源は交換済みなので、残りは基板ですが、基本的に12V系のデバイスが多いので電源パターンは12Vです。5V電源は別に配線しています。バイパスコンデンサが12Vラインの直ぐ上にあり、写真右のような感じで間隙が少ない所もあります。8枚とも、間隙を広げておきました。ギリギリ離れていた所が筐体内の温度上昇で接触するということは考えられます。
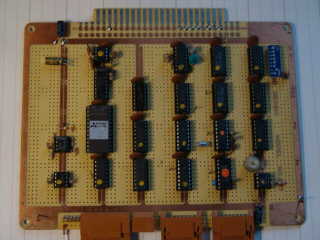
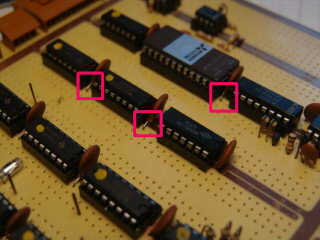
アマゾンで殺菌灯と蛍光灯センサライトを購入しました。DCOの音源テーブルを作るのにUVEPROMのイレーザが必要です。
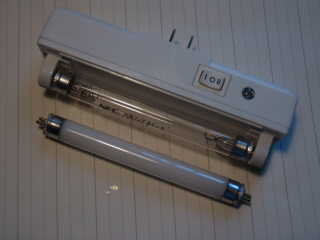
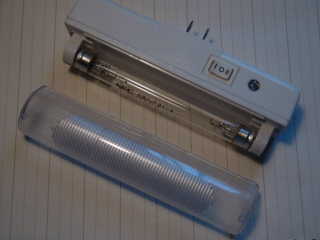
先週、厚紙で作製した型を元に1mm厚のアルミ板から基板取り付けパネルを作製します。右のユニバーサルはLED駆動基板です。EG/ARは2色LEDを使うため、カソードコモンのLED駆動回路を追加します。
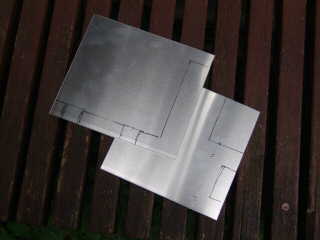
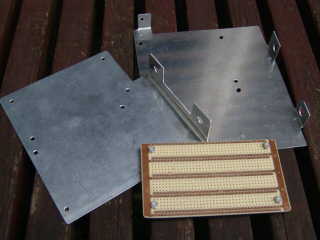
旧EG基板を取り付けて寸法を確認します。良いようです。
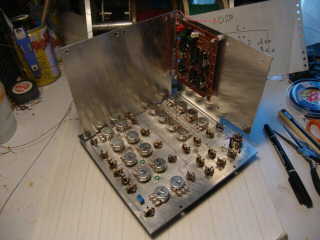
秋月から16ステップアナログシーケンサ用の部品が来ました。現在、10ステップのアナログシーケンサで演奏テンポを制御していますが、本来は0~Fまでの16段階の指定ができます。新たにここに載っている16ステップシーケンサを作製予定です。
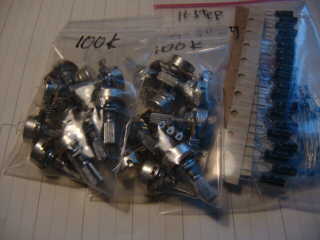
9月5日
シーケンサの部品といっしょに購入した、SSRです。早速、DCOの不具合検出ボードに取り付けました。
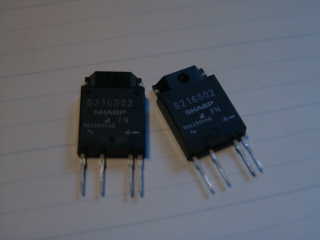
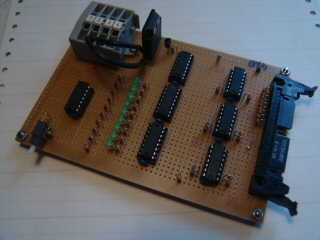
Ebayで購入した16ステップアナログシーケンサ用の4000シリーズのCMOSデバイスです。4箇所から購入しましたが、1箇所からまだ届いていません。

ダンボール箱で簡易BOXを作り、ROM消去してみます。ROMライタが無いので結果はアパートに帰ってからです。
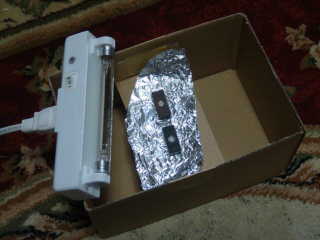
SSRを追加したDCO不具合検出ボードで不具合発生時にDCOの電源が切れるか実験します。動作良好です。
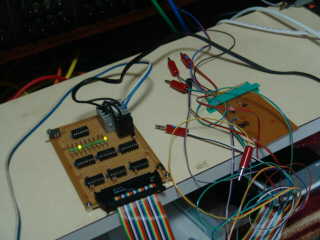
DCO横の新モジュール2のパネルのドリルセンタ図を作成します。
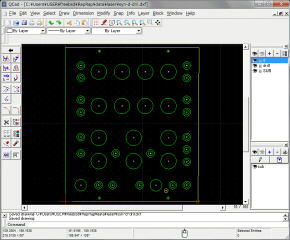
HeeksCNCでGコードを生成します。
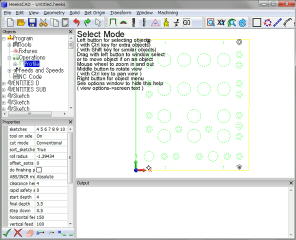
生成されたGコードをレーザ用のデータに変換して、NCVCで確認します。
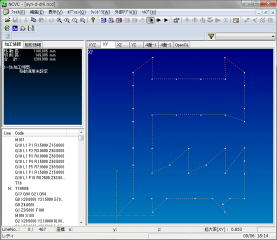
レーザ加工機でドリルセンタを刻印します。
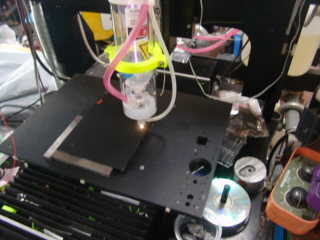
手動でセンタポンチを打って、ボール盤で穴開けします。
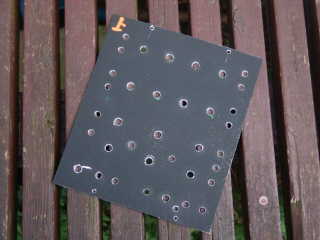
塗装を落として、サンドペーパで表面処理します。
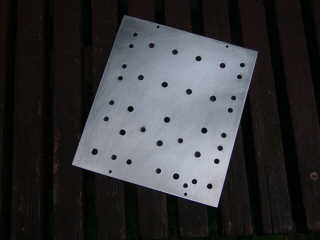
つや消し黒の缶スプレーで塗装します。
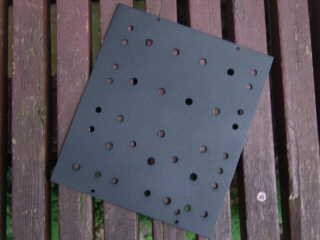
SSRを追加した不具合発生検出基板を接続して、丸半日以上稼動させてみました。気温が下がったためか、現象は出ませんでした。
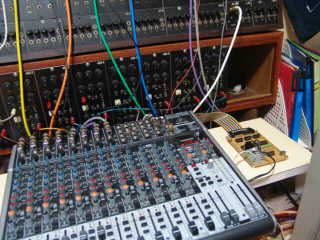
9月6日
新ユニットのEG部の動作テストを行います。ちょっと配線が間違っていました。修正して動作良好です。
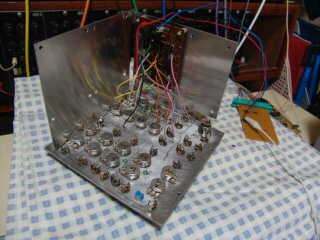
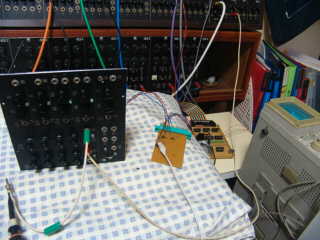
LED駆動基板を配線して点灯確認します。
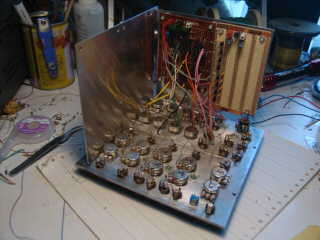
ROM消去のダンボールBOXにふたを追加して紫外線が漏れないようにアップグレードしました。
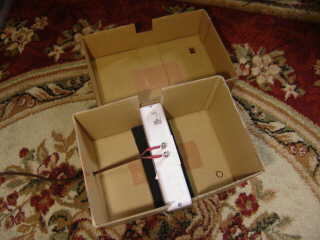
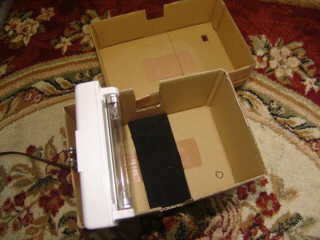
新ユニットにLFO、ARx2基板を追加して、動作確認しました。
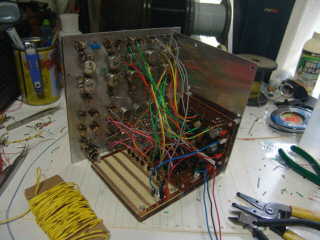
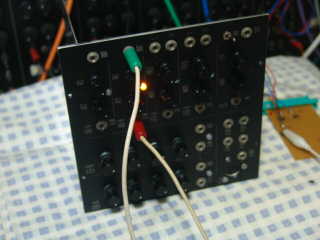
続いて、LFO、ジョイステック、レベルシフト基板を追加して、動作確認しました。配線がちょっと間違っていましたが、修正して、動作良好です。
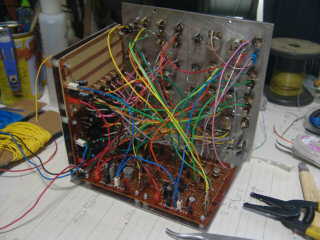
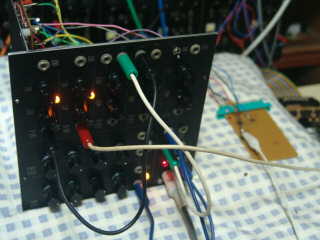
9月7日
VCA用のコネクタから新ユニット用の電源を追加します。
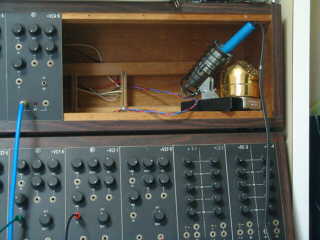
新ユニットを組み込み、動作確認をします。EG、AR、LFO、ジョイステックです。動作良好です。
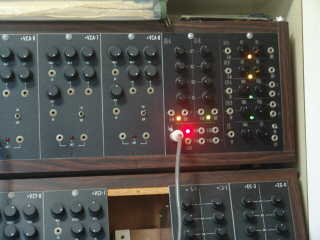
新ユニット2の刻印の原稿です。
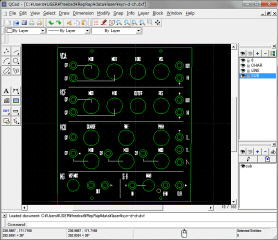
HeeksCNCにDXFファイルをインポートします。CHARとLINEを全てスケッチに変換して、プロファイル処理をします。ポストプロセス後、Gコードを保存します。
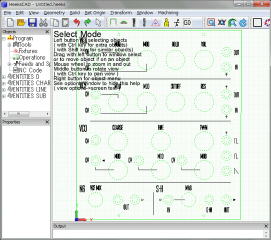
レーザ加工機用データに変換して、NCVCで確認します。
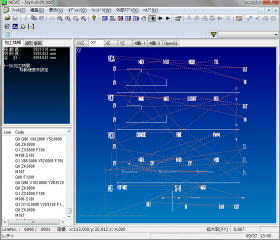
新ユニット2のパネルに刻印を行います。
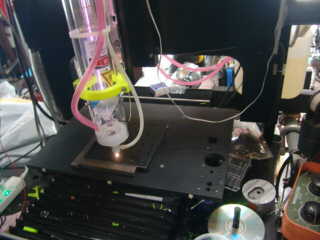
残念ながら、失敗しました。移動範囲が以前の3Dプリンタの設定になっていたため、Y方向が足りなかったです。
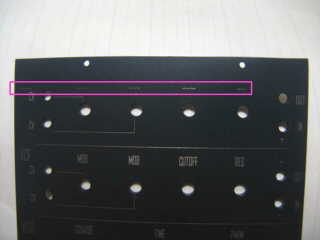
こちらはMSP430用のaitendoで購入したLCD用のフレキ変換ボードにコンデンサを追加します。9個のコンデンサが必要です。
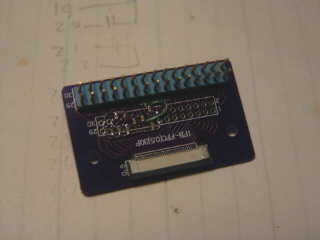
新ユニット2で使用する、VCO、VCF、VCAの基板と部品を旧パネルから取り外しました。
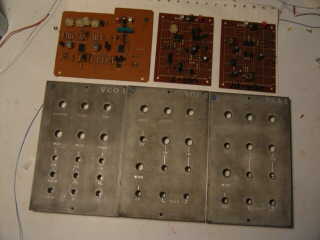
9月8日
こちらも新ユニット2で使用するノイズジェネレータとS/H回路を新たにユニバーサル基板に作製します。S/Hは専用のICのLF398を使用します。動作確認を行いました。
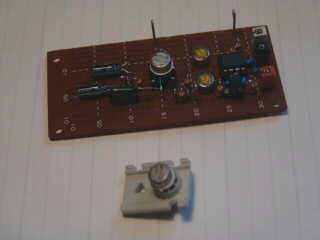
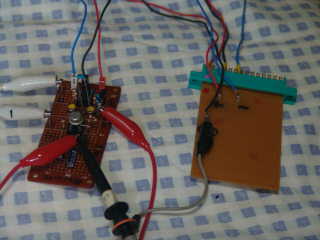
16ステップアナログシーケンサ用の残っていたCMOSが届きました。ロジックは珍しい24ピン幅広の4514です。これでCMOSのロジックが全部揃いました。
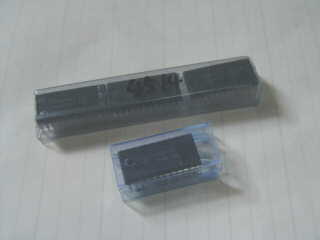
失敗した新ユニット2のパネルの刻印をやり直します。剥離剤で塗装を剥がして、缶スプレーで塗装します。
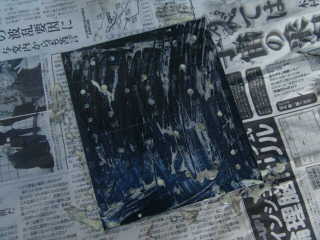
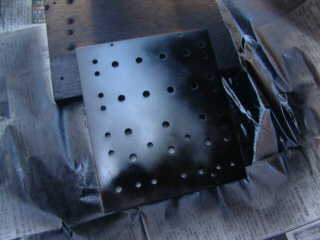
塗装が完了しました。
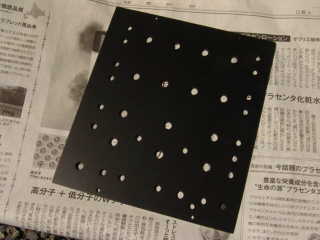
基板取り付け用の1mm厚のアルミパネル加工して、仮止めします。
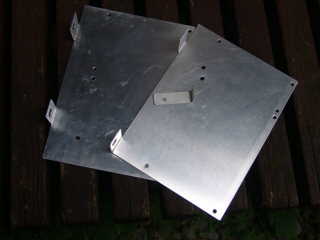
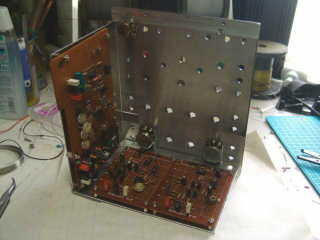
レーザ加工機のファーム(Marlin)のリミッタ設定を変更して、刻印し直しました。今度は成功です。
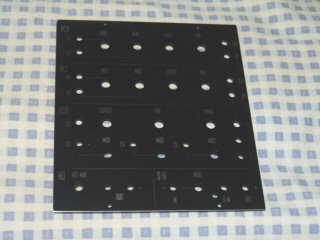
パネルに部品を取り付けます。
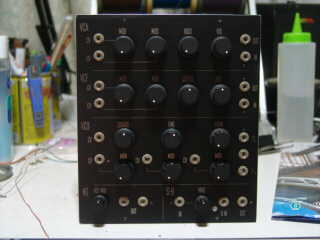
9月9日
DOCの横に仮止めします。
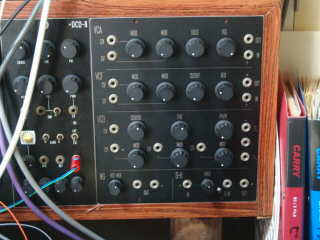
パネルと基板間の配線を行います。VCFとVCAの配線が完了たところ。本数が結構多く大変です。
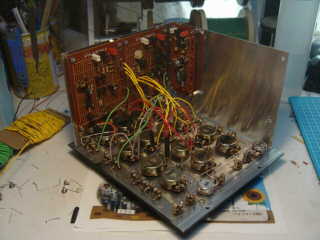
9月10日
新ユニット2用の電源をDCO用のマザーから引き出して接続し動作確認を行います。動作良好なので、筐体に組み込みました。新ユニット2はVCO、VCF、VCA、NG、S/Hです。
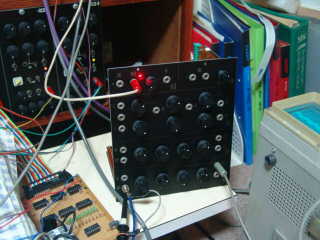
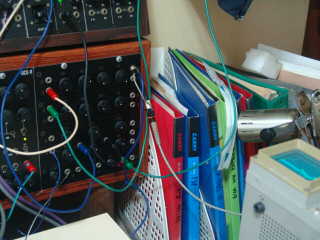
新ユニット1、2が完成したので、全体の写真を撮ってみました。35年以上経って空きスペースが埋まりました。ディレイド・モジュレータの出力をDCO(ビブラート)に使った曲を録音しました。データはこのサイトのトリオソナタです。SMFから変換プログラムでデータ変換しました。クリックでMP3がダウンロードできます。BWV525-1、BWV525-2、BWV525-3です。
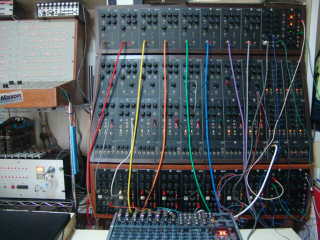
MC-80+のCV出力が不安定になる件です。8chのうち半分がダメです。
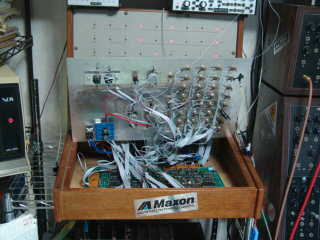
MC-80+の内部では上記のノイズジェネレータ、S/Hでも使用した専用ICのLF398使用しています。手持ちが幾つかあり、プラスチックパッケージとCANタイプの2種類があります。今回はCANタイプを使用しています。ホールド用コンデンサ端子は空中配線しているため、リード線を加工して交換してみましたが、現象変わらず、直りませんでした。デバイスは壊れていなかったです。
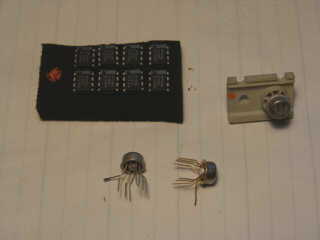
オシロでS/Hのアナログ電圧とサンプルパルスの入力波形を見ても正常で、少し悩みました。色々調べてると、どうもホールド用コンデンサのリーク電流が増えているようです。試しに1chのみコンデンサを交換したところ、正常動作しました。フイルムコンデンサも経年劣化で大幅にリーク電流が増えるようです。正常動作していると思っていた半分もリークが多く、リフレッシュ中でも僅かに電圧が下がっていることが分かりました。8ch全てコンデンサを交換する予定です。
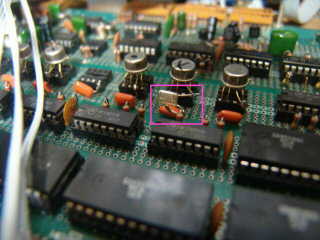
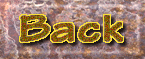
